Scope Pressure Equipment Inspection and Testing
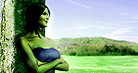
Our scope of work encompasses, Air Receivers, Accumulators, Boilers, Condensors, Digestors, Heat Exchangers, Autoclaves (medical & industrial), Deaerators, Steam Jacketed, Vessels, Reactors, Industrial Pressure Cookers, etc. i.e. any Vessels that fall within the criterion of the Acts.
Our preparation work encompasses; Boiler & Heat Exchanger tube cleans, either Hydroblast or mechanical or both. Chemical clean of accumulators and Air Receivers, Stripping and opening of all relief valves, valves and appurtenances. Stripping of door interlock facilities. Complete stripping or disassembly of any pressure vessel prior to test and inspection the spading, blanking or plugging of all vessels including inspection covers, mud holes, hand holes etc. Obviously the vessels are reassembled and commissioned after the performance of any test.
We are able to currently undertake the following:
- Hydrostatic testing up to 1300 bar
- Ultrasonic Thickness Surveys
- Endoscopic Internal Examinations
- Translation of visual internal & external inspections
- Preparation and completion of inert gas tests
- Magnetic Particle Crack Detection
- Dye Penetrant Crack Detection
- Radiographic Weld examination
- Hammer testing
- Relief valve calibration
- Pressure Gauge calibration
- Pressure Vessel Internal Coating
- Recertification of Pressure Vessel
- Design reviews of Pressure Vessels
- Design reviews of pipe systems
- Design vs as built reviews or audits
- Material traceability in terms of manufacturers certificates
- Material identification by various methods
- New Designs and Design Verification
- Pressure Equipment Commissioning