About us
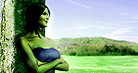
MISSION STATEMENT
We wish to continue to provide our clients with an ethically achieved result incorporating the highest level of integrity in all aspects of our inspection examination test and certification.
This will be done at a fair and reasonable rate allowing for sustained profitability, existence and continued growth of the company and its employees, also allowing expansion and duplication in all area's of the country.
To remain competitive with the continued incorporation of the latest technology and training in all facets of the company and its employees.
Above all to remain the market leaders and trend setters and continue to set the industry standards by example to our clients and competitors alike.
BACKGROUND INFORMATION
Since the inception of Vessel Inspection in 1977, the company has had an average growth in turnover of some 25 % per anum. This growth has been restricted to the operation of one central office in Johannesburg from where we cover many regions. Vessel Inspection contracts work in each and every province throughout the country. We work in every corner of the country from Piet Retief to Port Nolloth from Messina to Port Elizabeth.
The nature of our business, as set out in more details elsewhere in this document, is such, that it is a legal requirement to have qualified registered personnel inspect, asses and certify pressure vessels and a legal requirement that on a regular or cyclic basis every pressure vessel in any industry, and includes such industry as mining, food processing, mineral process, automotive, pharmaceutical, petrochemical and many others, must be subject to a full inspection and certification process every year, bi yearly or three yearly depending on the category of industry.
THE TEAM
Vessel Inspection Services now employs 16 permanent staff at this time, as well as contract staff as and when required. Our staff compliment comprise of the following:
- Engineers, IPE, CP/PV and CP/SE(CP/B)qualified for inspection & certification, mostly contracted out
- Technicians, 8 teams of up to 6 persons each, on contract.
- Sales and Marketing, 4 telesales and representatives for site visits.
- Admin, 3 persons involved in day to day office duties including database
maintenance and capture of new information, typing of tenders and quotes,
invoices and Test Certificates.
- Accounts, 1 person involved in Debtors & Creditors and accounting tax
procedures.
- Management comprises of Managing Director, Financial Director, Operations
Director, General Manager, Sales & Marketing Manager, Technical and
Inspection Manager.
Notes: During major plant shutdowns we employ temporary staff drawn from the
various Industrial Artisan Hire companies. These persons are used
exclusively for preparation and reassembling work. Our existing permanent
technicians become site management agents only.
TECHNICAL CAPABILITIES
Our scope of work encompasses, Air Receivers, Accumulators, Boilers, Condensors, Digestors, Heat Exchangers, Autoclaves (medical & industrial), Deaerators, Steam Jacketed, Vessels, Reactors, Industrial Pressure Cookers, etc. i.e. any Vessels that fall within the criterion of the Acts.
Our preparation work encompasses; Boiler & Heat Exchanger tube cleans, either Hydroblast or mechanical or both. Chemical clean of accumulators and Air Receivers, Stripping and opening of all relief valves, valves and appurtenances. Stripping of door interlock facilities. Complete stripping or disassembly of any pressure vessel prior to test and inspection the spading, blanking or plugging of all vessels including inspection covers, mud holes, hand holes etc. Obviously the vessels are reassembled and commissioned after the performance of any test.
We are able to currently undertake the following:
- Hydrostatic testing up to 1300 bar
- Ultrasonic Thickness Surveys
- Endoscopic Internal Examinations
- Translation of visual internal & external inspections
- Preparation and completion of inert gas tests
- Magnetic Particle Crack Detection
- Dye Penetrant Crack Detection
- Radiographic Weld examination
- Hammer testing
- Relief valve calibration
- Pressure Gauge calibration
- Pressure Vessel Internal Coating
- Recertification of Pressure Vessel
- Design reviews of Pressure Vessels
- Design reviews of pipe systems
- Design vs as built reviews or audits
- Material traceability in terms of manufacturers certificates
- Material identification by various methods
- Design Verification
- New Designs
- Pressure Equipment Commissioning
INSPECTION TECHNIQUES FOR INTERNAL & EXTERNAL EXAMINATION
A variety of None Destructive Examination methods are employed to assess the condition of pressure vessels and pipe systems in accordance with the original design codes or design requirements. These methods are completed by experienced and qualified personnel. In some cases, particularly in the case of lagged or painted pressure vessels or pipe systems some surface preparation may be required, however, all possible attempts are made to avoid major restoration or repair requirements.
The following should be noted:-
1) The degree or extent of inspection of a pressure vessel or pipe system varies with the application and the operating conditions.
2) Thorough visual examination by suitably qualified personnel is the most universally used method of inspection.
3) Corrosion, erosion, abrasion or any deviation from specification or design codes should be established.
4) Preliminary internal inspection may reveal unsafe conditions such as loose internals, corroded components, off spec components.
5) A thorough inspection should cover every aspect of a vessel or pipe system including corrosion, erosion, mechanical damage, hydrogen blistering deformation, lamination or delamination and or cracking.
Other methods to assist in the evaluation, examination and inspection may encompass the underlisted:-
1) Dye Penetrant testing for indicating the presence and extent of any cracks or surface defects, however, good surface preparation is imperative.
2) Magnetic particle testing is also used for indicating the presence and extent of cracks and surface defects but obviously can only be employed with materials having a magnetic property. Preparation requirements are not as severe as Dye Pen.
3) Radiographic testing is employed to detect internal imperfections in materials or welds by passing gamma or x-rays through the material and recorded on film. Some surface preparation may be required.
4) Ultrasonic thickness testing is employed to gauge material thickness to spec, internal corrosion & pitting. This is the most useful method to gauge installed pipe wall thicknesses to design specs. Ultrasonic thickness meters are calibrated on site to cater for different materials.
5) Acoustic emission testing is usually employed on heat exchangers and other equipment employing tube bundles and is used to determine the locality of internal leaks.
6) Hammer testing is employed as an audio method of determining cracked vessels or pipe systems.
7) Intrascopic internal inspections via endoscope may be employed for internal inspections in inaccessible vessels or pipes.
8) Leak testing may be employed incorporating soap bubbles, smoke, water, nitrogen and helium.
9) Conventional hydrostatic or Pneumatic pressure testing is also employed for leak detection.
10) Metallurgical assessment and review.
a) Shall include a thorough examination of material certificates and the manufacturers identification marking.
b) Quantitative sorting, separation and positive identification of all
materials using hardness testing, magnetic properties and spark
testing.
c) Quantitative chemical analysis using x-ray fluorescence.
d) Metallographic examination by microscopy and by replication of surfaces.